Product Introduction
Pioneer Thermal can design LED heatsink based on customer's requirement, then build LED heatsink prototype to production. Most LED heatsink are made by extrusion, cold forging and die cast process.
LED heat sink made by die cast process:
Available heat sink process of Pioneer Thermal:
Main Process | Extrusion | Bonded Fins | Skived Fins | Snapped Fins | Folded Fins | Heat Pipes |
Cold Forging | Die Casting | FSW cold plate | Gun drill cold plate | Vacuum brazing cold plate | Vapor chamber | |
Finishing Processes | CNC machining | Drilling | Tapping | Stamping | Anodizing | Screen printing |
Powder coating | Laser etching | Polishing | Electrophoresis | E-coating | ||
Finishing Value Added | Embedded fans | Thermal Greases | Screws | Springs | Clips | Embedded heat pipes |
Phase change materials | Back plates | Gap filler pads | PEMs | Standoffs | Dielectric pads | |
Compounds |
Pioneer Thermal Quality Assurance:
Pioneer Thermal will do the quality control from incoming material to heat sink shipped, if customer find any defect parts when received the goods, we will send replacement or credit note.
Inspection tool of Pioneer Thermal:
Heat sink dimension | |||||
CMM | Projector | ||||
Heat sink performance | |||||
Salt Spray Tester | Pressure Tester | Clip Force Tester | Drop Tester | Helium Leakage Tester | |
Heat sink reliability | |||||
Wind Tunnel | On Line Thermal Tester | HP Qmax Tester | HP Delta T Tester | Thermal Shock | High Temperature Aging Chamber |
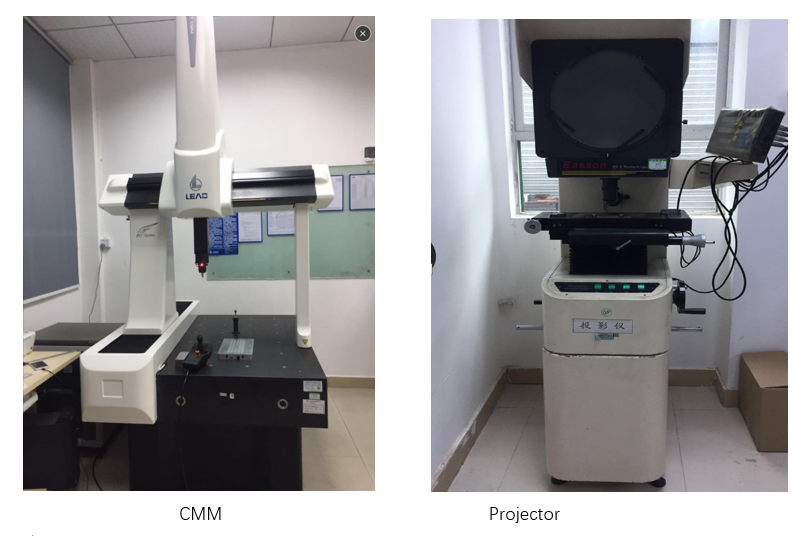
Pioneer Thermal R&D:
About Pioneer Thermal:
As a heat sink manufacturer in China, Pioneer Thermal is certified with ISO9001, ISO14001 and TS16949 with 7500 square meter facility, and has a dedicated quality assurance department with full CMM capabilities. We are focused on providing advanced technology, superior customer service and outstanding value to our industry partners.