Custom heatsinks play a crucial role in various industries by providing tailored thermal solutions to meet specific requirements. Following is an overview of custom heatsinks.
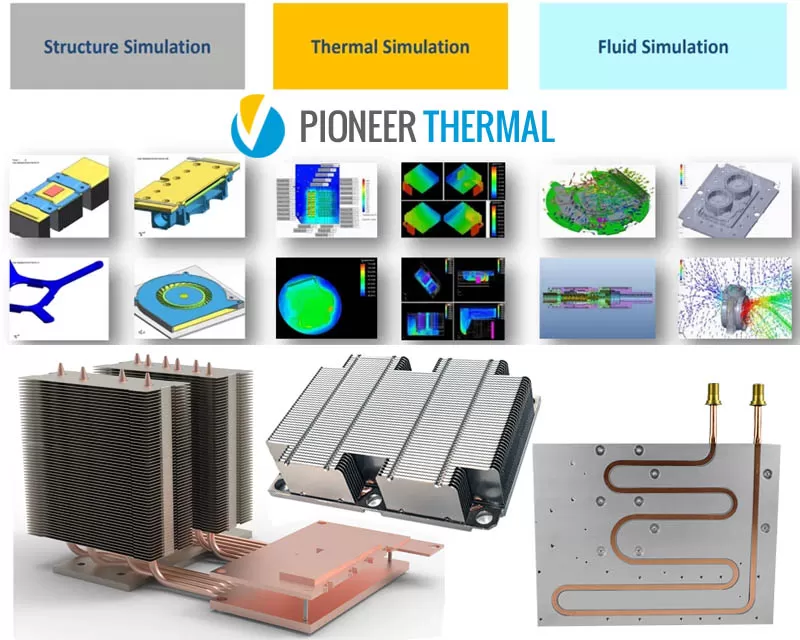
Importance of Custom Heatsinks
● Meeting Specific Requirements: Different electronic devices and systems have unique thermal management needs. Custom heatsinks can be designed to precisely fit the size, shape, and heat dissipation requirements of a particular device, ensuring optimal performance. For example, in space - constrained electronic enclosures such as handheld devices or embedded systems, custom heatsinks can be designed to efficiently dissipate heat from tightly packed components.
● Enhancing Performance: By custom - designing heatsinks, it is possible to improve the overall performance of electronic devices. For high - heat - flux devices such as power electronics or high - performance processors, custom heatsinks can incorporate advanced cooling technologies like heat pipes or vapor chambers to effectively remove heat and prevent overheating, allowing the devices to operate at higher speeds and with greater reliability.
● Ensuring Reliability: In harsh environments such as military applications or industrial settings where electronics are exposed to extreme temperatures, moisture, dust, or shock, custom heatsinks can be engineered to provide reliable thermal protection. They can be designed to withstand these challenging conditions and ensure the long - term stability and functionality of the electronic equipment.
Design and Manufacturing Process
● Feasibility Evaluation: The design process of custom heatsinks usually begins with a no - cost feasibility evaluation of the proposed design. This involves using software to model and analyze the thermal performance of the heatsink, providing an initial indication of its viability.
● CFD Modeling: Next, a computational fluid dynamics (CFD) model is created to simulate the heat transfer and airflow around the heatsink. This helps in optimizing the design to achieve the best thermal performance and ensuring that it meets the specific requirements of the application.
Prototype Testing: After the design is optimized, a prototype of the custom heatsink is produced. Prototype testing is essential to validate the thermal, shock, and vibration performance, as well as to ensure a proper fit within the intended device or system.
● Manufacturing: Once the prototype is approved, the custom heatsinks are manufactured in a state - of - the - art facility. Various manufacturing techniques such as extrusion, stamping, forging, die - casting, and CNC machining may be used, depending on the material and design requirements.
Applications
● Electronics Industry: Custom heatsinks are widely used in the electronics industry to cool components such as CPUs, GPUs, power amplifiers, and electronic boards. They help in maintaining the temperature of these components within the safe operating range, improving the performance and reliability of electronic devices.
● Telecommunications: In telecommunications equipment, such as base stations and routers, custom heatsinks are used to dissipate the heat generated by high - power transmitters and other components. This ensures the stable operation of the equipment and helps in reducing signal interference caused by overheating.
● Automotive Industry: With the increasing use of electronic systems in vehicles, custom heatsinks are required to cool automotive electronics such as engine control units, power inverters, and battery management systems. They play a crucial role in ensuring the safety and reliability of these systems, especially in high-performance electric vehicles.
Pioneer Thermal has skilled in-house engineers to offer no-cost thermal design service and customize your heat sink design and effective manufacturing based on your requirements. Get custom heat sinks with 24h DFM feedback. Free feasibility check & prototype. Provide us with your drawings, and we will offer a professional assessment.
- Custom Heatsink
Tags :