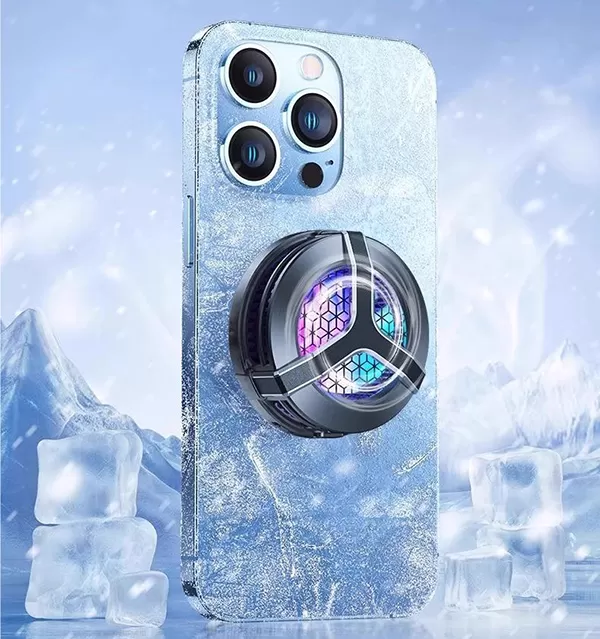
1. Efficient thermal conductivity: Use materials with high thermal conductivity, such as aluminum alloy, copper, etc., to ensure that heat can be quickly conducted to the surface of the heat sink and effectively dissipated.
2. Multi-channel design: Multi-channel design is usually used to increase the heat dissipation surface area, improve heat dissipation efficiency, and ensure that the equipment can maintain a stable temperature even when operating under high load.
3. Heat sink design: Usually a fin structure is used to increase the heat dissipation surface area, speed up heat conduction and dissipation, and improve heat dissipation efficiency.
4. Compact design: Adopting a compact design to ensure efficient heat dissipation in a limited space, it is suitable for a variety of equipment and scenarios.
5. Cooling fan: Some conductor heat sinks are also equipped with cooling fans. Through the auxiliary heat dissipation of the fans, the heat dissipation is accelerated, the heat dissipation efficiency is improved, and the stable operation of the equipment is ensured.
The idea behind conductor heat sinks is to protect equipment from overheating damage, extend equipment life, and improve equipment performance and stability.Pioneer Thermal engineers have long been aiming to carry out thermal analysis to obtain efficient and reliable systems,so we can create functional thermal solutions that meet the demanding cooling requirements in the most efficient and cost-effective way possible.