Copper skived fin heatsinks are high-performance cooling solutions widely used in electronics, LED lighting, power supplies, and high-power applications. The skiving process allows for the creation of ultra-thin, dense fins with excellent thermal conductivity. Following is an overview of the manufacturing process.
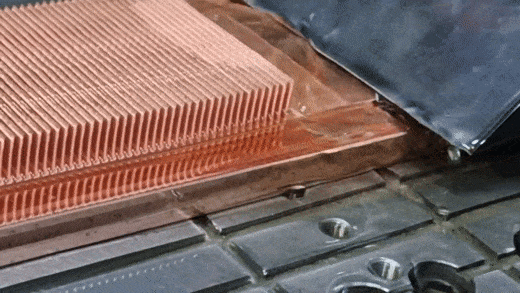
1. Manufacturing Process of Copper Skived Fin Heatsinks
A. Material Selection
High-purity copper (C1100 or similar) is preferred due to its superior thermal conductivity (~400 W/m·K).
The copper block must be defect-free to ensure smooth skiving.
B. Skiving Process (Key Step)
A sharp, precision skiving tool removes thin layers of copper from a solid block in a peeling motion.
The fins are formed in one continuous piece, ensuring a seamless base-to-fin connection (no thermal interface resistance).
Fin thickness can range from 0.1mm to 1.0mm, with heights up to 50mm or more.
The process allows for high fin density (up to 40 fins per inch) for superior heat dissipation.
C. Fin Straightening & Shaping
After skiving, fins may undergo straightening to ensure uniform spacing.
Optional secondary machining (milling, drilling) for mounting holes or custom shapes.
D. Surface Treatment (Optional)
Nickel plating (for corrosion resistance in harsh environments).
Anti-oxidation coating (to prevent tarnishing).
Solderability enhancement (if needed for assembly).
E. Quality Control
Dimensional checks (fin thickness, height, flatness).
Thermal performance testing (thermal resistance, heat dissipation efficiency).
Pressure drop testing (for forced-air cooling applications).
2. Advantages of Copper Skived Fin Heatsinks
● High thermal performance (better than bonded or stamped fins).
● Seamless base-fin interface (minimizes thermal resistance).
● Lightweight yet robust (thinner fins without sacrificing strength).
● Customizable designs (variable fin height, density, and shape).
3. Applications of Copper Skived Fin Heatsinks
High-power electronics (IGBTs, power semiconductors).
LED lighting (high-lumen applications).
Telecom & servers (5G base stations, CPU/GPU cooling).
Automotive & aerospace (EV battery cooling, avionics).
A. Material Selection
High-purity copper (C1100 or similar) is preferred due to its superior thermal conductivity (~400 W/m·K).
The copper block must be defect-free to ensure smooth skiving.
B. Skiving Process (Key Step)
A sharp, precision skiving tool removes thin layers of copper from a solid block in a peeling motion.
The fins are formed in one continuous piece, ensuring a seamless base-to-fin connection (no thermal interface resistance).
Fin thickness can range from 0.1mm to 1.0mm, with heights up to 50mm or more.
The process allows for high fin density (up to 40 fins per inch) for superior heat dissipation.
C. Fin Straightening & Shaping
After skiving, fins may undergo straightening to ensure uniform spacing.
Optional secondary machining (milling, drilling) for mounting holes or custom shapes.
D. Surface Treatment (Optional)
Nickel plating (for corrosion resistance in harsh environments).
Anti-oxidation coating (to prevent tarnishing).
Solderability enhancement (if needed for assembly).
E. Quality Control
Dimensional checks (fin thickness, height, flatness).
Thermal performance testing (thermal resistance, heat dissipation efficiency).
Pressure drop testing (for forced-air cooling applications).
2. Advantages of Copper Skived Fin Heatsinks
● High thermal performance (better than bonded or stamped fins).
● Seamless base-fin interface (minimizes thermal resistance).
● Lightweight yet robust (thinner fins without sacrificing strength).
● Customizable designs (variable fin height, density, and shape).
3. Applications of Copper Skived Fin Heatsinks
High-power electronics (IGBTs, power semiconductors).
LED lighting (high-lumen applications).
Telecom & servers (5G base stations, CPU/GPU cooling).
Automotive & aerospace (EV battery cooling, avionics).
In electronics, effective thermal management is crucial. Our copper skived fin heatsinks offer a top - notch solution. Ready to enhance your product's thermal performance? Let's connect and find the right heat sink solution for your project.