
This heat dissipation structure of IGBT modules with pin fins is applied to IGBT modules. IGBT is the abbreviation of InsulatedGateBipolarTransistor. IGBT devices are the core of power converter devices and are widely used in electric/hybrid vehicles, rail transit, variable frequency appliances, power engineering, renewable energy, smart grids and other fields. Their main function is to convert DC power into AC power, which is a key component of power electronics. One of the most important high-power mainstream devices.
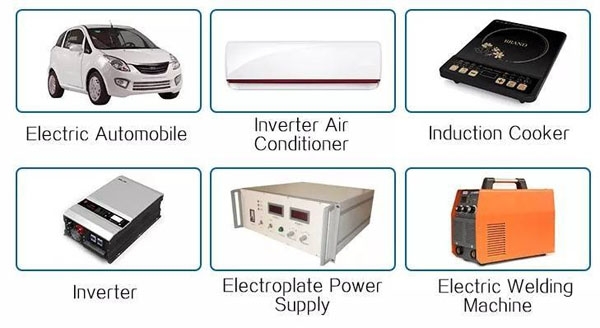
At present, major well-known IGBT device suppliers have successively launched automotive IGBT chips, and fine trench gate technology has become a mainstream technology. Domestic devices such as Star, BYD and CRRC Zhuzhou have also begun to replace imports in large quantities in the field of new energy vehicles, achieving large-scale application and having a certain industrial foundation.
As trench technology matures, trench refinement plays a key role in improving the overall performance of medium and low-voltage IGBT chips for electric vehicles. In new energy electric vehicles, the supporting motor controllers have higher power levels, and the heat dissipation requirements for the inverter are also increasing. Inverters using pin fin (pin fin) structure can obtain greater The heat dissipation area effectively ensures the safe operation of the inverter.
The heat dissipation column type substrate can realize water cooling and efficient heat dissipation of the IGBT module. The heat dissipation column type (Pin-Fin) substrate includes a heat dissipation base plate. The inner surface of the heat dissipation base plate has grooves for forming a liquid cooling water channel after being bonded with the IGBT module. IGBT The pin fins of the module are located in the groove. The heat dissipation bottom plate is provided with a first seal and a second seal between the outer peripheral side of the groove and the IGBT module. The heat dissipation bottom plate is provided with a first seal and a second seal between the first seal and the second seal. Annular groove, one side of the annular groove fits the IGBT module, and is connected to the outside world through the through hole on the outer surface of the heat dissipation base plate.
Al/SiC (aluminum silicon carbide) composite material is a new type of IGBT heat dissipation material. It is currently notarized as a material that can provide a good thermal expansion coefficient, greatly improving the performance of IGBT power modules. Tested to extend product life by 5 times.

Pioneer Thermal can design the heat dissipation column (Pin-Fin) substrate into needle-shaped and arc-shaped shapes according to customer needs. The heat sink design process mainly includes the following content. First, determine the type, size, model, etc. of the parts to be processed, and generate parts drawings. At the same time, analyze the craftsmanship in CNC machining, determine the process route of CNC machining, and then Clarify the content of each process of CNC machining, and finally select CNC parameters and processing tools. Our first step will be to carry out forging according to the design requirements in the order of rough machining, semi-finishing and finishing, and the machining accuracy will gradually increase. In this way, on the one hand, the metal removal rate is improved, and on the other hand, the uniformity requirements of the finishing car are met. The inner and outer surfaces of the substrate are roughed first, and then the inner and outer surfaces are finished. Due to structural mechanical strength and other considerations during the forging process, some nozzles will be produced, which need to be removed by CNC milling to facilitate subsequent processing. During the CNC machining process, in order to control deformation, we use secondary processing to remove stress and reduce product deformation to the greatest extent possible. We can also provide the required surface treatment from sandblasting anodizing to electroplating, including making it into the popular gold color currently on the market.