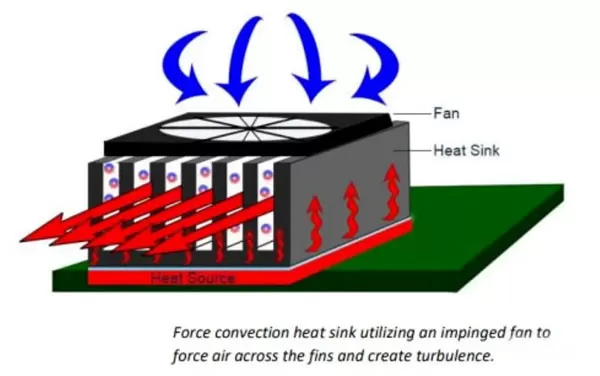
Extruded aluminum is one of the most popular and cost-effective manufacturing methods. The size of the extruded heat sink varies depending on the application, which is smaller for plate level applications and larger for medium power applications. They can be designed for passive or active cooling based on the shape and spacing of the fins. Board level extruded heat sinks are common in packaging such as BGA and FPGA.
The selection of a suitable extruded heat sink largely depends on the desired shape. Extruded heat sink is made by creating a profile mold that determines the density, spacing, and length of the fins, as well as the height and width of the base. Softened aluminum is pushed into the mold to form a long rod called the original rod, which has the same contour and size as the mold. Then cut the bar into smaller standard shaped bars/rectangles or custom lengths. These are further processed and refined to create customized heat sinks. This process is fast, cost-effective, and scalable. That's why many people first consider extruded heat sink when looking for a thermal solution.